Martijn Stiphout, Wooden Surfboards
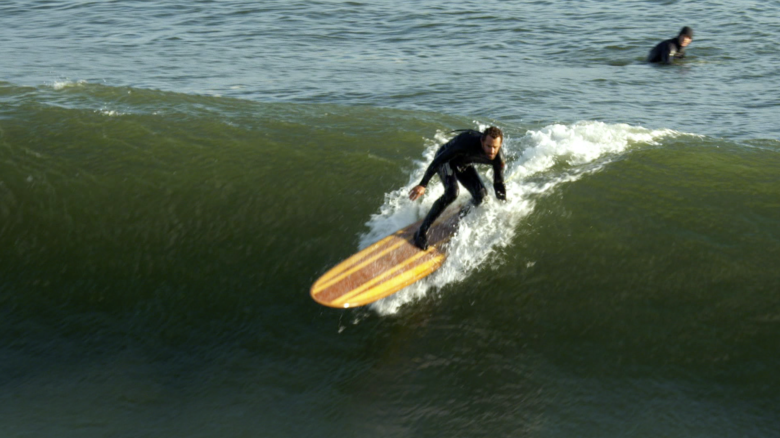
Martijn Stiphout
Stiphout started surfing while living in the Netherlands, so when he decided to relocate to the States in 1993, California was the ideal location. With a degree in Marine Biology from Monterey Bay State University, he is as passionate about ocean conservation as he is about riding the waves.
His dedication to conservation is what gave him the idea to try to lessen his impact on the environment by handcrafting lightweight, one-of-a-kind, wooden surfboards, focusing heavily on sustainable and recycled materials.
Have you always worked with your hands?
I got my first pocket knife when I was 5 years old. I used to whittle little flutes out of willow branches. And, I can remember making small boats on vacations with my family. I once took bamboo reeds and twine and made a boat with a leaf for a sail. It travelled for about a mile on a river in Holland when we were on holiday there.
What drew you to your chosen craft?
Necessity. I started building my own surfboards after the last of my used foam boards broke while I was surfing. I chose wood as it allowed me to create a much sturdier board than one made of foam. I was also able to get reclaimed wood for free. I loved the process of building wooden boards and decided to make a career of it.
What do you enjoy most about your craft?
I get tremendous satisfaction from taking trash and turning it into treasure. Taking someone else’s old materials and turning them into a functional finished product that’s even higher quality than a traditionally manufactured product is very cool.
How long did it take you to become an expert?
I’m learning all the time. I started building boards six years ago, and each board is better than the last. So, given that I can keep improving my designs and skills, I don’t know that I’ll ever consider myself an expert. I’ve built 90 wooden boards to date, and I hope to build a thousand more.
Do you feel like you are still learning?
Yes. For example, I recently learned how to use a laser to get more precise and lighter results for the internal frames of my boards. And, just a few months ago, I learned how to pickle wood using a solution of rusty nails and vinegar. It’s like a natural stain that brings out the tannins that are in certain woods. Really beautiful.
How many hours do you spend making each item?
Quality craftsmanship takes time. My bodysurfing handplanes each take about 10 hours. The hollow, wooden surfboards take about 60 hours over the course of a month. Some of the smaller wood products l make, like our Save-A-Surf Box, take about an hour. Lots of work, but lots of reward, too.
If you could spend a day with a master of your craft (past or present), who would it be and why?
Bob Simmons. He was a great craftsman and a great surfer. He built displacement, planing hulls to use as surfboards, and he was putting fins on boards before almost anyone else. In the early 1940s he had fins on his boards. There’s a picture of him in 1946 on an 8-to-10 foot wave just hauling across the face on a twin fin, 9’6” hull. Back then people went straight down a wave, but Bob was cutting across the wave at top speed. Amazing.
Is there any one person who has bought/used any of your products that makes you especially proud?
Everyone who buys a Ventana product has a unique, personal story. But, I think I get the most inspiration from younger kids who are stoked to bodysurf on my handplanes.
What does the future hold for your type of work? Are you training young people in your craft?
Wooden surfboards are making a comeback. They are better for the environment, last longer and surf really well. I expect we’ll see more innovation with wood going forward…bringing together traditional woodworking styles with modern, surfboard construction methods. Personally, I’ve been using lots of historic woods of late. For instance, we recently obtained some redwood from the author, John Steinbeck’s house in Pacific Grove, California. I’ve been using that to make some beautiful surfboards.
I’ve taken on a few interns in the past, but I’m most proud of Alena Horton.
She built a beautiful, sunburst design longboard with me when she was only 14 years old! She even rode it to the finals in the “Women of Waves” surf contest in Capitola, California.
Why is it important for people to make things with their own hands?
Making something yourself, gives you a deeper connection with what you use. You value more the time and craftsmanship that goes into the item, and that has a tendency to make you more conscious about what you buy and use in your life. We live in a world of disposable consumption. Making things with your hands can help to change that.
In what ways are handmade goods better than those that are mass-produced?
The thought and care that goes into something that’s handmade makes people respect and appreciate the item more. And, getting up close and personal with an item as it’s being made almost ensures higher quality.